Without Compromise
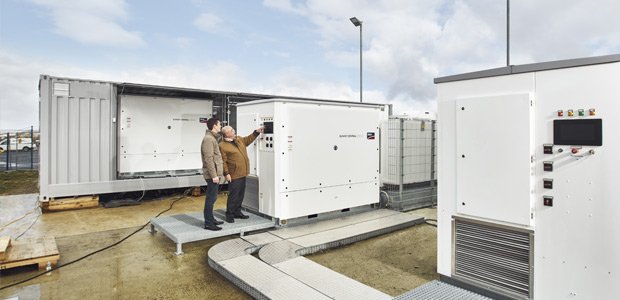
In sunny regions, large-scale solar farms are already generating electricity a lot more cost-efficiently than coal-fired or nuclear power plants. Experts are forecasting that the cost of photovoltaics will continue to decrease, making them the most important energy source worldwide – a goal Bernhard Voll is passionately pursuing. He travels all over the world for SMA, making large-scale PV farms even more efficient and reliable.
Specialists can do more than generalists
Two huge gray containers, large white switch cabinets and a whole lot of cable – Bernhard Voll is in his element here. The engineer is in charge of SMA’s global medium-voltage business, and the containers with the slightly cumbersome name Medium Voltage Power Station 5000 are his “youngest offspring.” They are currently undergoing rigorous testing at SMA’s own PV farm at the company headquarters in Niestetal, hence all the cable. On the journey from El Salvador to Tokyo, Voll discusses the latest test results with project manager Jan-Hendrik Welzel.
The Medium Voltage Power Station contains all the technology required to convert direct current from PV modules into grid-compatible, three-phase current in large-scale PV power plants, feed it reliably into the high-voltage grid and support the grid in the process. “All components in the container, from the central inverter and the transformer to the switchgear, are perfectly coordinated with each other. The container solution allows our customers all over the world to build large-scale PV power plants of the highest quality in a minimum amount of time and at low cost,” underlined Voll. “A version featuring one inverter and an output of 2,500 kW is already on the market and is now being followed by this solution with two inverters in one container, supplying double the output.”
Partnership offers everything from a single source
One partner SMA is working with on the transformers and switchgear used in the container solution is Siemens. But the partnership between SMA and Siemens in the PV power plant business goes far beyond pure product solutions, as 56-year-old Voll explained: “Our customers can rely on the joint expertise of two specialists for planning, building and operating their plants. This is a clearcut advantage, for example when it comes to successfully taking part in auctions for new power generation capacity and ensuring that this capacity can be connected to the electricity distribution grid without any issues.”
An increasing number of countries in regions throughout the world are organizing auctions like this to guarantee a reliable and cost-effective electricity supply. Tenderers that provide the lowest prices per kilowatt hour of electricity supplied are awarded the contract. In bidding processes in the southern U.S., in Latin America and in Arab countries, large-scale PV power plants are already significantly beating the costs of using traditional energy generators like coal, oil and gas.

At the SMA PV farm, Jan-Hendrik Welzel and Bernhard Voll appraise the test progress of the new Medium Voltage Power Station.
Quality pays off
Voll strongly rebuffs the widely held conception that this is only possible if you use the most cost-efficient components: “PV power plants need to deliver a reliable supply of electricity over decades. If the individual components within the complex system technology don’t work together properly, the system will never be able to realize its full capacity. This also translates into losses for the operator if, for example, part of the system breaks down as a result of poor component quality or reliability.”
For a large-scale PV power plant, which has 50 or more central inverters operating under challenging climatic conditions, such a breakdown means a substantial loss of sales. Against this background, it quickly becomes clear that it pays off to use tried-and-tested quality and sophisticated technology. “This is equally true for established markets in North America and Europe and future markets in South America, Asia, Australia, Africa and the Middle East,” said Voll, who spends 150 days a year traveling to different continents to explain the advantages of end-to-end system solutions to project developers, investors and PV system operators. “Each market has a different set of characteristics and peculiarities, which is why it is important for our solutions to work under all climatic conditions and across all utility grids.”
At SMA, this means that all types of inverters are intensively tested. At the company’s in-house test centers, engineers and technicians artificially age these devices, cover them with layers of ice in climatic chambers and heat them to over 50 degrees Celsius in extremely humid conditions. They also test their electromagnetic compatibility and behavior with a wide range of utility grids.
With this extensive array of tests, SMA not only ensures the highest in inverter quality but is also laying the foundation for them to be certified as compliant with international technical standards by independent inspection companies. With the Sunny Central 2500 for instance, SMA was the first manufacturer to obtain both the essential UL-62109 certification for the North American market from the independent testing institute Underwriter Laboratories (UL) and IEC standard 62109-1/2 certification for global markets from Bureau Veritas for a central inverter featuring 1,500-volt technology – something that is becoming increasingly important internationally. “Independent confirmation of compliance with valid technical standards is required in many important markets. And certification both simplifies and speeds up the implementation of power plant projects, for example through simplified approval procedures,” said Voll.

Bernhard Voll and Jan-Hendrik Welzel are looking forward to seeing the first largescale PV power plants to use the Medium Voltage Power Station 5000.
Only real tests produce reals results
This means that, with the Sunny Central 2500, project developers can save on costs in two ways: through certification and through the 1,500-volt technology. Compared with conventional 1,000-volt technology, it reduces system costs in large-scale PV power plants considerably because the higher voltage means that more modules, among other things, can be connected to the inverters.
Two of these powerhouses are contained in each of the Medium Voltage Power Stations, which are currently being tested under real-life conditions at SMA’s PV power plant in Niestetal. Voll is exceptionally proud of the test facility: “None of our competitors have anything like this. They usually simulate tests and interactions between the individual components merely using a computer, which is like comparing a flight simulator with flying a real airplane.”
“Furthermore, it is not uncommon for the real-life tests at our test centers and in the PV farm to produce results that deviate from the computer simulation. After all, we are dealing with highly complex technology that is used in the open air and is thus subjected to all kinds of weather conditions. Perfect coordination between components sets the highest standards when it comes to design,” added Jan-Hendrik Welzel. He is extremely pleased with the test results displayed by the Medium Voltage Power Station 5000 so far: “When the station goes into serial production soon, our customers can be confident that they will be getting a system that has been coordinated down to the smallest detail and that will produce maximum yields at minimum costs for at least 25 years.”
Voll has no doubts about this either: “I’m confident that we will see the container solution in widespread use in countries from America to Asia within the next few years.” But for now, he has to head off to Tokyo where another Medium Voltage Power Station is waiting to be presented to a Japanese trade audience.
This article was first published in Annual Report 2016.
Feel free to contribute!