Think Opex*
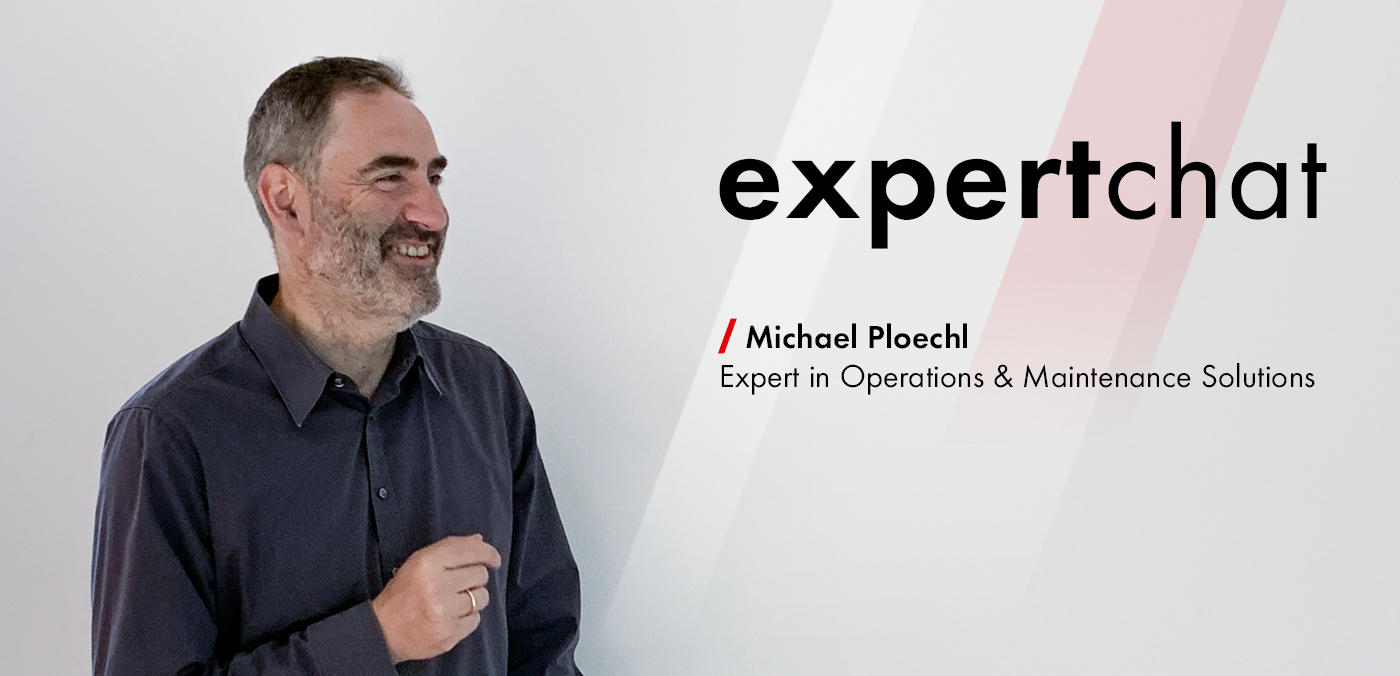
Storage and PV power plants are system relevant and the energy transition cannot succeed without them. If a power plant fails, the costs mount up very quickly. Michael Ploechl is the head of the SMA monitoring center Germany, and he and his team ensure that it doesn’t come to that. At the two SMA Monitoring centers located in the U.S. and Germany, expert teams analyze the system performance of power plants worldwide 24/7 in real time. The professionals in USA and Germany ensure that everything runs smoothly. In our interview, he explains why operating expenditure is more important than capital expenditure and how rabbits occasionally cause him some trouble.
How does your working day at the O&M Center normally begin?
We usually begin with acute cases. That is a good warm-up and often gives us new impetus too. Today I discussed approaches to remedying communication problems in a back-up system in Spain with a colleague. Communication difficulties and insulation defects are among the most frequent sources of faults in power plants.
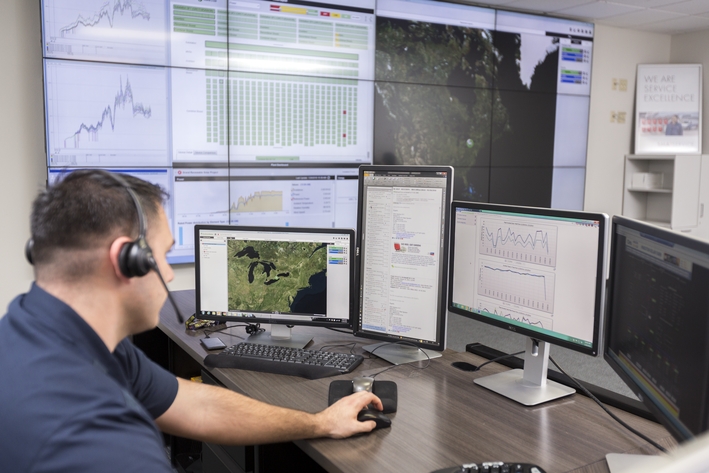
In the two monitoring centers in Ulm, Germany and Rocklin, California, SMA monitors solar and storage power plants worldwide around the clock.
Why is the continuous monitoring of power plant operations so crucial?
The failure of individual components or even the entire power plants goes hand in hand with a loss of energy supply, which nobody can afford or wants.
In PV systems and PV power plants, a failure means losing energy and feed-in power. The operator loses revenue for the energy that cannot be supplied and used. With smaller plants that rely on energy self-sufficiency with solar power, the energy must then be bought from an external source at a high price.
In storage power plants, a lack of available power can often be equated with an unstable utility grid. In some circumstances, this results in “penalty payments” to the grid operator because the power plant did not supply the power that was promised. It can quickly become very expensive. That is why we monitor the storage power plants around the clock.
What are the most common reasons for yield losses and what does O&M do to counter them?
Preventive maintenance is always the best way to avoid a failure in the first place. Our technically experienced teams can even precisely predict forthcoming failures of individual components. They can detect the first signs of an upcoming defect and replace the affected component before it fails.
But if a component does fail, we detect it very quickly with our monitoring centers in Ulm, Germany and Rocklin, California. Covering all time zones worldwide enables us to respond with all due speed. Our customers really appreciate that.
Who are your customers and how do they become aware of you?
We often take care of operation and maintenance for owners of or investors in the power plants, with whom we also work in the project business with. They are familiar with the quality of our systems and know that we are very experienced. But we are also increasingly being approached by operators who previously had no idea that we offer these services for third-party components too. They request it precisely because we have impressed them with our services in other areas or they have heard about it from others. Of course, that is pleasing for us because recommendations are high praise indeed.

It is worth taking a proactive stance to the performance, as regularly maintained PV and storage power plants generate up to 30% more power.
How do the services for PV and storage power plants differ?
The requirements for a storage power plant are far more complex due to the batteries that are connected. They must be able to supply energy around the clock. That is why monitoring 24/7 is also fundamental. But as a basic principle, all systems in our portfolio receive the same level of attention and are optimally maintained.
That extends right up to the performance guarantee, which we use to assure our customers that they can expect a certain minimum level of system availability. We ensure that by carrying out our monitoring. If performance is below average or the system fails, we put it back into operation as quickly as possible. The range then extends from a simple parameter adjustment to on-site service. Where target performance is not achieved, we pay a compensation to the customer depending on the contractually agreed performance level.
From what point does O&M pay off?
Good service always pays off, because every system should be operated as smoothly and efficiently as possible throughout its entire service life.
For rooftop systems with power of up to 100 kWp, the local solar power professional is sure to provide good service.
But larger systems or power plants in the megawatt range call for a professional O&M service provider. This is because here there are many other aspects to bear in mind besides simple system monitoring, such as workplace safety, remote maintenance options, data security to international standards or communication to the electric utility company.
Are there regional differences or challenges?
There are some, yes. For example, in the U.S. and Canada, systems are far larger than in Europe or Asia. The environmental regulations differ greatly due to local conditions, sometimes even within a single country. Safety is extremely important for servicing, but the topic of occupational safety and health is dealt with very differently in different regions. There are a number of challenges. But we would not be here if we could not rise to every challenge. Here, our global service network is a clear advantage, because it means we are familiar with the challenges in each region and enables us to act accordingly.
What sets SMA O&M Solutions apart from the competition?
SMA has been active on the PV market for 40 years now and we can draw upon experience gained over all that time. Within our company, more than 500 employees develop hardware and software solutions, and we are familiar with the project business from day one. As a result, we know exactly what is important and where there may be pitfalls. We keep the entire service life of the system in mind and highlight potential for optimization to our customers so that they can operate their systems and power plants even more efficiently. This ranges from small details, such as improving system performance by coating or sealing the PV modules, to holistic modernization solutions that extend the service life of the system and maximize yields. If you have been acquainted with a system for a long time and think outside the box, you know how to make it work best for the customer.
How do the SMA O&M Centers at Ulm and Rocklin work together?
At the handover times, we ensure a detailed exchange of information on the current status. In the process, we go through any noteworthy aspects of the day and check through all of our systems for a seamless handover. Then one team goes home and the other starts work.
What is the most curious job you have had?
Technically, there isn’t really anything that couldn’t be resolved one way or another. But things often become curious when nature comes into play. For example, once a population of hamsters had settled in the area of a power plant in Germany. As the animals are protected by nature conservation, we assumed responsibility for monitoring the common hamster as well.
From time to time, rabbits are found to be digging their burrows beneath system components in some regions. That poses real challenges. In general, animals seem to love inverters. We have already had beehives, bird’s nests, rats and snakes in the enclosures. So-called pest control is an often underestimated challenge. Because what often looks cute in pictures can actually jeopardize the efficiency of the power plant.
What aspect of your job do you particularly treasure?
I particularly like the fact that no two days are ever the same. One small technical issue sometimes brings entirely new aspects and solutions into play. Luckily, we can draw upon a huge amount of experience and meet almost any challenge as an international team. That is a nice feeling.
And then, of course, I love eating cake together on birthdays. Unfortunately, we have missed out far too much in that respect during this coronavirus pandemic. The first birthday cake after the pandemic will have to be all the bigger to make up for it.
What would be essential for making everyday life in O&M easier?
Communication that is 100 percent stable. Because that would rid us of most of the susceptibility to faults. And anticipatory maintenance that detects faults before they occur wherever possible. But we are already working on that with predictive maintenance.
*Operating expenditure As distinguished from CAPEX (capital expenditure).
SMA Operations & Maintenance: tailored solutions for higher yields
Regularly maintained PV and storage power plants generate up to 30 percent more power. To ensure a maximum return, it is therefore worth taking a proactive stance when it comes to the performance of the power plant. SMA Operations & Maintenance services help you achieve maximum yields and system availability. With a portfolio boasting a nominal system power of more than 4.5 gigawatts, SMA is one of the world’s best O&M service providers.
Feel free to contribute!