Saltwater, Chemical Plant, Monsoon: No Match for the SMA Fault Detective
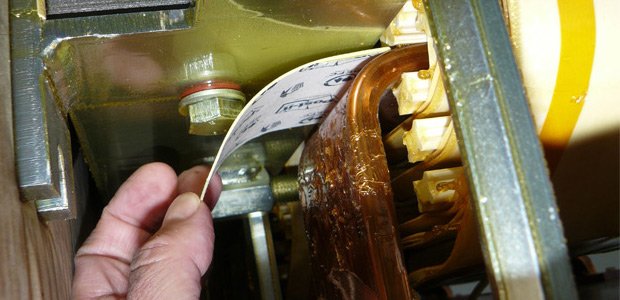
Seals, rust protection, flawless insulation: Reinhard Lehmann, an analysis engineer, has been focusing his efforts for eight years now on helping SMA equip Sunny Central inverters for even more effective outdoor use. One of his responsibilities is ensuring that these high-performance central inverters are fit for outdoor use—at all times, anywhere in the world.
SMA’s site in Niestetal is home to a central inverter testing center—the only one of its kind in the world—where the largest members of the SMA product family are put through their paces. This means they can be positioned anywhere in the world —even in the most adverse of conditions. But sometimes, the devil is in the detail and, as is the case with any technical device, inexplicable challenges may initially be encountered here, too.
If an inverter ever fails to run as it should—due to extreme conditions, for example—Reinhard and his colleagues in the Service department are immediately on the scene to analyze the fault and the environment in which it occurred. This keeps operations running indefinitely over the long term, whatever environmental forces are at play. Reinhard particularly enjoys dealing with cases involving corrosion and chemical reactions that trigger changes in the material. In fact, he has become known as an SMA expert in this field—and not just within the walls of the testing center.
It gets Even Better: Optimizing Central Inverters
A challenging case where environmental influences caused extreme damage to central inverters at a facility belonging to TATA Power in India, located at 22°24’29.09″N 68°59’28.39″E, also landed on Reinhard Lehmann’s desk. These Sunny Central inverters are located just a few hundred meters from the ocean, and the white crests of the Arabian Sea sometimes reach as far as the devices. A chemical plant is also situated directly behind the PV system, from which residue is also often recovered on the inverters. The third challenge is monsoons. Twice a year, the region is pounded for several weeks by heavy rain and humidity as high as 98%, which presents a real challenge even for rigorously tested central inverters.
As the humidity level found in this system presented a risk of choke failure, Reinhard Lehmann got in touch with employees in the Indian Service department via a video conference. He illustrated on screen how they should go about looking for the source of the fault to find the cause of the humidity. After this detailed training, they quickly found what they were looking for: the insulation wasn’t thick enough to withstand the dripping, chemical-enriched saltwater was the culprit. The fault was quickly remedied.
Solutions Are Transferred to Serial Production
Reinhard Lehmann was pleased: “After we applied wider insulation to a specific spot [see photo above], the Sunny Central devices in this system have since then already withstood two monsoon seasons and have been working perfectly.” Naturally, SMA has applied this solution to serial production. “This means that Sunny Central devices are now that much more resistant.”
Reinhard Lehmann is of course continuing his mission of identifying and rectifying “corrosion incidents” and is always happy to receive any information about systems at extreme inverter locations equipped with Sunny Central inverters.
Do you want to find out more about what happens to our Sunny Central inverters in the testing center? Then you may be interested in the following articles:
Off to Munich: Sunny Central in High Altitude Test
Sand and Dust: Sunny Central CP in a Stress Test
Unique Testing Center for Hybrid Energy Supply Systems in Operation
Feel free to contribute!