Life tests increase the reliability of PV inverters
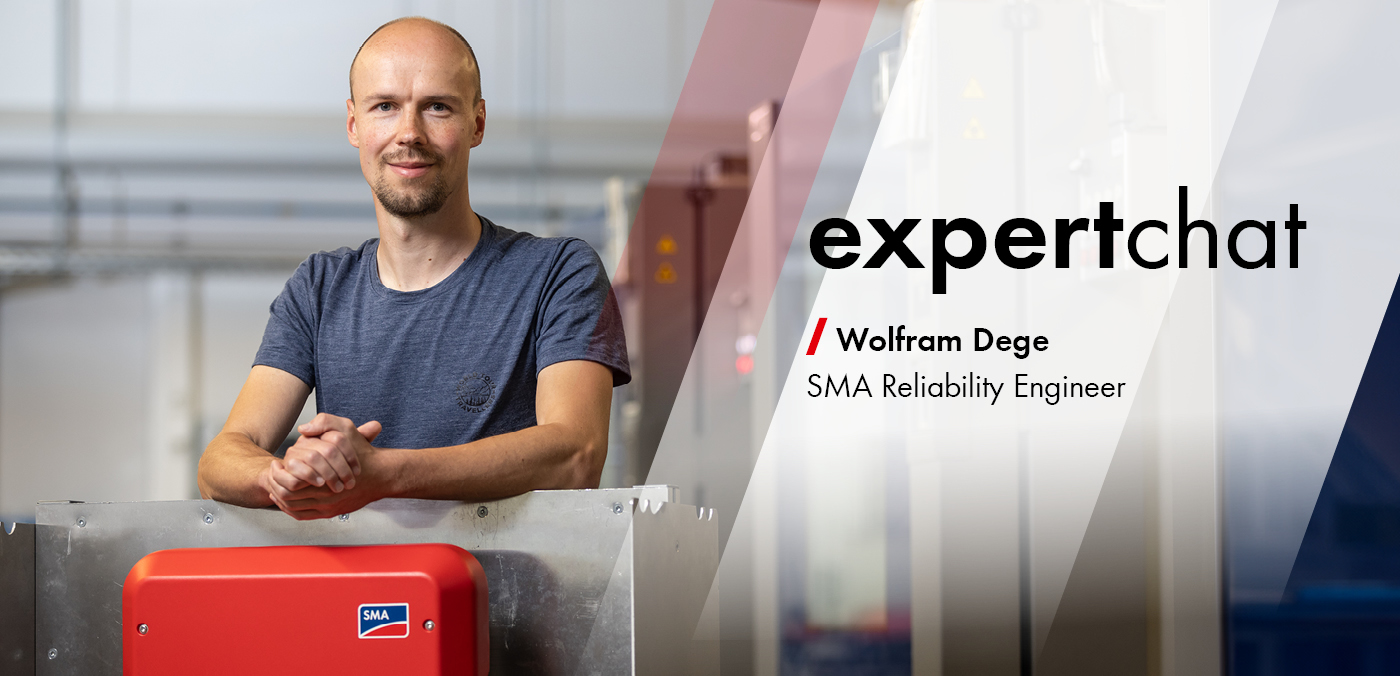
Wolfram Dege destroys inverters for a living – and helps to make them better in the process. To do so, he puts the devices under high stress and induces artificial aging. He really puts the inverters through the wringer, using cold, heat, moisture and high currents and voltages – ideally all at once. This gives him valuable information about service life. Read on to find out more about his life-prolonging work and his favorite test.
Wolfram, what exactly does a reliability engineer do, and how did you become one?
Put simply, it’s my job to destroy things, but in a very deliberate way. More accurately, I take the products developed by SMA – so mostly inverters and their components – right to the limits of their endurance until they fail. I think it must have something to do with my innate personality traits. Right from an early age, I would take anything I could get my hands on and play around with it, bend it and generally go to work on it until it was ruined.
How do you break inverters?
I use climatic chambers, heating cabinets, power sources and special test setups to subject inverters to heat, cold, changes in temperature, moisture, voltage and current until they fail so that I can identify their weaknesses. In short, when the devices come to me, they go through all the stresses that they could be exposed to in use by customers.
Isn’t destroying inverters the opposite of what a reliability engineer is meant to do?
Destroying products is not an end in itself. Robert Bosch once said that anything that was still in one piece after testing obviously hadn’t truly been tested because we don’t know what its limits are. In my field, technical reliability, it’s a matter of trying to induce specific failures as a means of gleaning information about the service life of equipment. That means I try to look into the future to determine when the device I’m investigating would be expected to fail if a customer used it perfectly normally.
When is a product deemed reliable, and what happens if a product doesn’t pass your tests?
If the prediction made on the basis of the tests is acceptable, the device will be considered reliable. If the predicted service life is too short, however, I will take that information to the product developer and we will work together to think about what we can do to make the device more durable. For example, in cases like that, we might turn to alternative components or more robust materials. The improved device will then undergo repeat testing until the expected service life for customers meets our requirements.
How can you validate a 20-year device service life in such a short period of testing?
SMA generally requires service lives of between 10 and 20 years. Obviously, no company can afford to run tests in real time before selling the product. That’s why we perform accelerated life testing at SMA. I can speed up material aging by increasing the intensity of various stresses, such as heat. It’s not about destroying the devices in unnatural ways, such as by choosing a very high test temperature that causes the plastics used to melt away. It’s more a case of recreating the same physical aging processes that happen when customers use the equipment – just at a much faster pace. That way, failures can be prompted much sooner in testing.
What is your role in SMA reliability testing?
My job is to develop custom accelerated life tests for our products, perform them and, once testing is complete, translate the results into meaningful conclusions about the equipment destined for use by our customers. The biggest challenge is applying the results of these highly accelerated tests to the operating conditions expected with our customers. To make these calculations, I create physical aging models and use tools and methods from the field of mathematics, especially statistics.
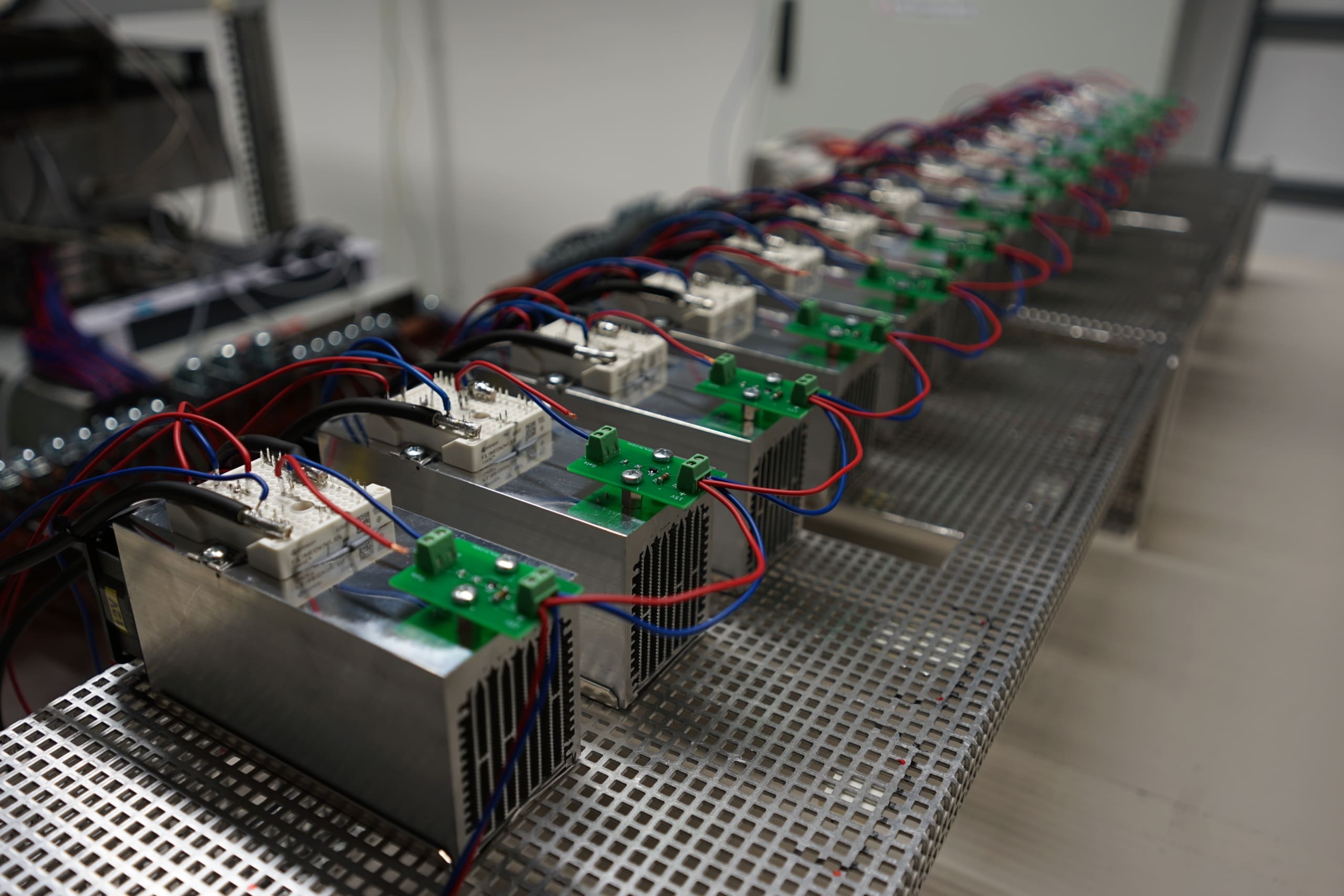
In the so-called power cycling test, semiconductor modules are subjected to high current and temperature variations.
Do the test results have an impact on the ongoing development of SMA equipment?
If the results of a test are negative, the first step is to discuss corrective actions and changes to the device as a means of directly improving the product. If the findings can be used to derive some general rules, these actions will also be incorporated into the various design guidelines that our development engineers use when working on new products. As a result, SMA inverters are getting more reliable all the time.
What is your favorite test and why?
There’s one test that exposes a device to an array of different types of stress at the same time, known as the SMA condensation test. In addition to cold, heat and changes in temperature, the devices are exposed to high humidity over an extended period. This generates a wide range of failure modes , each more intriguing than the last. With the right equipment, getting that on camera is a lot of fun. Preventing those failure modes from occurring calls for plenty of creativity and good teamwork with my colleagues in development. It’s a fantastic and varied challenge every time.
Hi Peter,
thank you for your friendly feedback. Actually we are working on these processes since years and it is an ongoing topic.
And you are right, it is crucial in the design phase to choose all components with an appropriate robustness margin to all relevant stressors and that’s part of SMAs reliability strategy. In this article we put the focus more on the testing point of view, but at the end a reliability concept succeeds when both aspects come together.
Best regards to Denmark, Wolfram
Hi Wolfram
Very good explanation of the test methods needed for improving reliability. The process you have described will take long time get a reliable product.
The first step is to design each part with the necessary robustness margin og all important parameters. Meaning temperature changes will change parameters in most of the electrical components and the circuit designer must implement the needed margin in the simulation of the design.
I know SMA are doing this, just miss it in the article. Br Peter