Climate Simulation at SMA Test Center
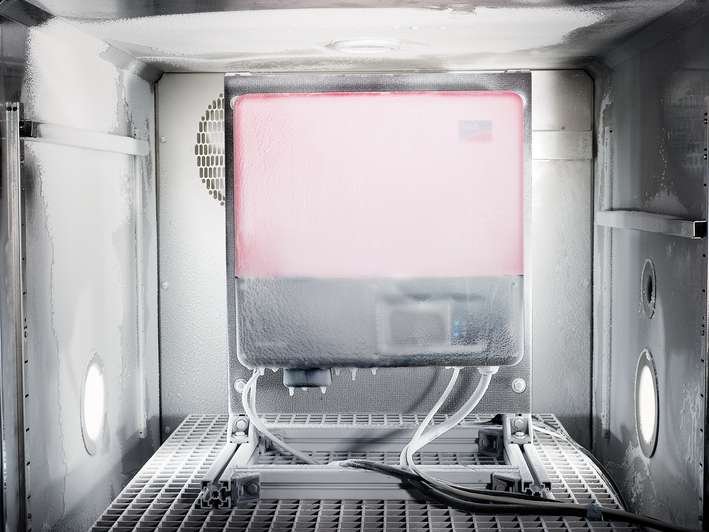
At the climate and stress laboratory the newly developed products are tested for reliability under extreme climatic conditions. SMA customers do not need to fear inverter damage due to freezing or overheating. We test the temperature limits for each new product.
The only exception in our laboratory are the Sunny Central inverters. Due to their size, we focus on assembly and component part tests. Other safety-relevant tests under climatic conditions can also be found in our test schedule. These tests already begin during a very early stage of development and are not completed until the devices from series testing are checked.
Shock frosting at -70°C
In building 11 and container 10 we can clearly see that temperatures can be distributed very differently. Since the laboratory temperature is still very agreeable, the conditions in the various cabinets for temperature, climate and shock testing are extreme. They can reach glacial levels of -70°C or sizzling +200°C. The units under test also have to endure the additional influence of very high humidity. Of course these are extreme conditions.
The tests are not strictly modeled according to real ambient conditions. To speed up aging and make predictions about possible failures after many years of operation, it is standard procedure to increase certain factors such as temperature, humidity, temperature increase or gradients.
Therefore, we test not just the inverters, but also the used component parts, such as capacitors, switches and transformers. This also helps to qualify the parts. The team for life cycle testing takes care of this task. Next to the normative test results, this is another important element for specifying the climatic profiles.
Desert or arctic: we simulate the world’s climatic zones
Another team, descriptively named “Internal Field Testing,” deals with the simulation of field conditions. Over the last three years, we developed and set up various test systems. Therefore these very complex simulations (such as day/night, summer/winter cycles) run almost completely autarkic.
What remains is the evaluation of the incoming flood of data. This enables reproducible results and allows us to compare inverters. It makes no difference whether we want to simulate arctic, tropical or desert climates.
It is required to fulfill certain standards to market our products. These standards are codified as norms. For electronic products, one focus is to protect consumers against the dangers of electrical energy. The required tests are performed by the Type Tests team.
This quick overview demonstrates what my colleagues and I deal with every day. There are always new challenges arising from the concurrence of temperature, humidity and complexity of SMA products. This requires appropriate expertise, but also willingness to learn and a certain degree of curiosity, to understand the physical and chemical correlations.
Over the last years, SMA has built the test center and continually expanded the capacities. Our development process benefits from the proximity and flexible access to the test locations. In addition, we focused our expertise on these tests. The quality of SMA inverters also profits from this.
Feel free to contribute!